Pharmaceutical Packaging
Healthcare-GettyImages-843421738-ftd.jpg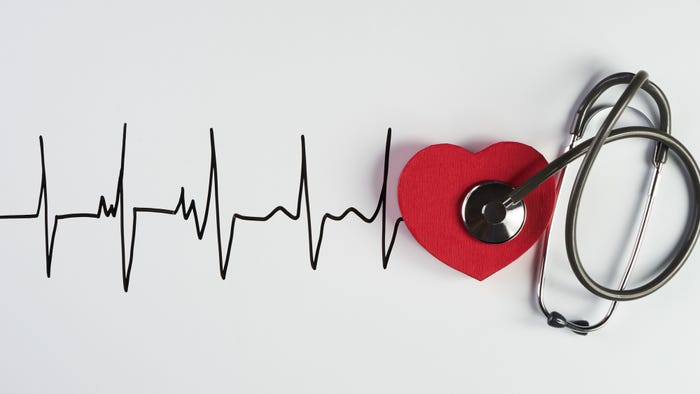
Pharma & Medical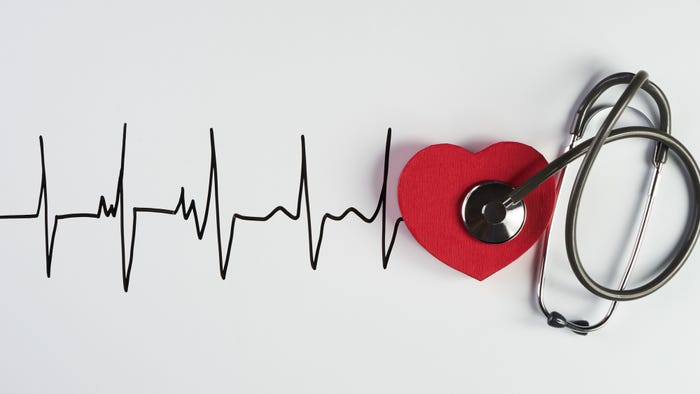
Healthcare Packaging News and Top IssuesHealthcare Packaging News and Top Issues
Earth Day and healthcare packaging sustainability, hospital packaging waste reborn as new products, label management tips for medicines, advancements in sterile medical packaging, more.
Sign up for the Packaging Digest News & Insights newsletter.